3-D printers offer better way to make some magnets
New method conserves expensive materials
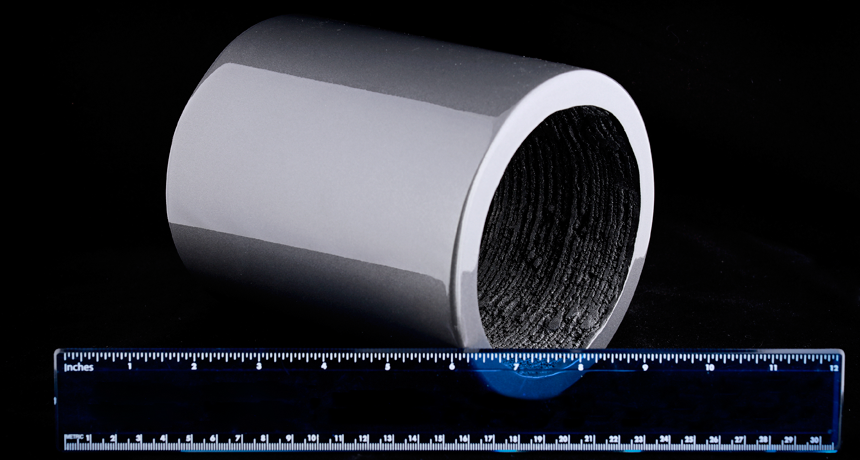
This magnet was created on a 3-D printer at Oak Ridge National Laboratory in Tennessee. (A ruler is shown for scale.) The method wastes less material than other ways of making magnets.
Oak Ridge National Laboratory
Powerful magnets are all around you. They’re found in electronic devices, ranging from speakers to the hard drives of computers. They’re also key to the many motors that keep an elevator or car working. They’re almost everywhere and in high demand. So scientists and engineers are chasing ways to improve them. And now a group of researchers have found a novel way. They build them with 3-D printers.
The magnets in all of these devices aren’t like the ones that you use to stick art on the fridge. These magnets are made of “rare earths.” These are a group of similar metallic elements that tend to be difficult to find and to mine in large quantities. That makes them expensive. So scientists would like to find ways to use these elements more efficiently.
Parans Paranthaman is a materials scientist at Oak Ridge National Laboratory in Tennessee. His group figured out a way to make strong magnets in any size or shape. These researchers used additive manufacturing. It’s a type of 3-D printing, where a machine “prints” a solid object by building it layer by layer, from the bottom up.
New devices — in everything from cars to cell phones — often need custom-shaped magnets, notes Paranthaman. One advantage of 3-D printing is that it lets people customize magnets to fit any project.
This type of manufacturing “gives you the ability to make these magnets in more complex shapes than are possible with conventional machining,” says Randy Bowman. He studies magnets at NASA’s Glenn Research Center in Cleveland, Ohio, and was not part of the new study. (NASA stands for the National Aeronautics and Space Administration.)
Paranthaman and his team printed “bonded” magnets. That means they contain magnetic powders held together with a polymer, molecules made from long chains of identical molecules. (A polymer tends to be plastic, resin or a related material.) Combining some magnetic material with a polymer means bonded magnets don’t break as easily as pure magnets.
Bonded magnets usually are made with a technique known as injection molding. That process involves heating the magnetic material until it’s liquid, then forcing it into a mold. When the liquid cools, it solidifies into the right shape. Injection molding is useful for making lots and lots of magnets that all have the same shape. But it’s not so great for making just a few magnets. That’s because it takes time, money and materials to build a single mold, even before the first magnet is made. Building the mold for an injection-created product to make just a single magnet would be like building a photocopying machine to copy just one sheet of paper.
Story continues below video.
Permanent magnets also can be made through a process called sintering. Here, the metal particles are heated and squished together until they stick. This produces a slab of magnet, which later must be cut and ground into the desired shape. Paranthaman says sintering can waste as much as half of the raw material.
His team described its new technique in the Oct. 31 Scientific Reports.
3-D printing, however, is good for small batches. The process lets inventors print magnets and test them. These tests help them find the best magnet design before going to the trouble and effort of building a mold. 3-D printing also may be useful to companies that only want to make a small number of magnets. And because 3-D printing directly forms the material into the shape of the magnet, it produces little waste. That’s important, in part, because the ingredients in bonded magnets tend to be so expensive.
Bowman says scientists are searching for ways to make less costly magnets. To do that here, they must use less of the magnet’s very expensive raw ingredients. And with 3-D printing, he says, “there tends to be less scrap.”
To nail down the 3-D-printing process, Paranthaman and his group took two years of trial and error. But their work paid off. They now they have a working recipe.
Their magnet-making process starts with magnetic pellets. These contain the elements iron, boron and neodymium (Nee-oh-DIM-ee-um) in powder form. Neodymium is a soft metal. It is also a rare earth. The pellets contain nylon, too. During the printing process, the machine heats the pellets, which melt into a liquid. That liquid passes through a nozzle called an extruder. It moves back and forth and right and left. As it does, the nozzle deposits each layer of the material at the proper spot to make the right shape. Once it finishes one layer, the nozzle starts to make another layer atop it.
Challenges still remain in printing magnets for real-world use. One big challenge is temperature. At the high temperatures at which a motor runs, for example, the magnetic field starts to weaken, Paranthaman notes. So his goal is to design a strong magnet that works well, even at high heat.
This is one in a series presenting news on technology and innovation, made possible with generous support from the Lemelson Foundation.