Chemists have unlocked the secrets of long-lasting Roman concrete
Small calcium-rich rocks help cracks in the material heal, experiments show
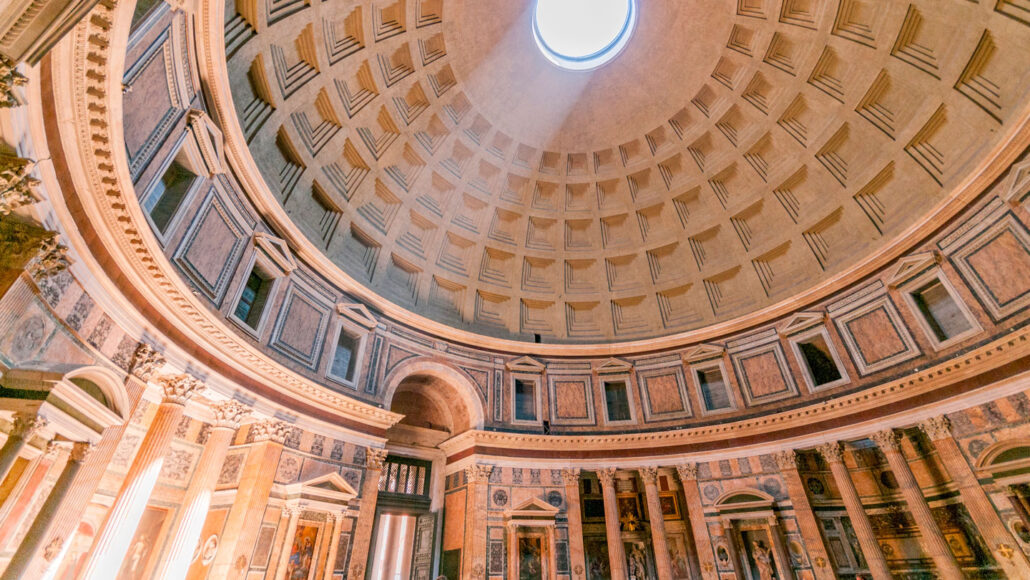
The Pantheon in Rome, Italy, was built around 126 A.D. from concrete. It still stands today, including its soaring dome (shown).
Stephen Knowles Photography/Moment/Getty Images Plus
Roman concrete has stood the test of time. Some ancient buildings still stand after millennia. For decades, researchers have been trying to re-create the recipe that made them last — with little success. Finally, with some detective work, scientists have figured what’s behind their lasting power.
Concrete is a mix of cement, gravel, sand and water. Admir Masic is a chemist at the Massachusetts Institute of Technology in Cambridge. He was part of a team that was trying to figure out what technique the Romans used to mix those ingredients.
The researchers suspected the key was something called “hot mixing.” It uses dry bits of calcium oxide, a mineral that’s also called quicklime. To make cement, that quicklime is mixed with volcanic ash. Then water is added.
Hot mixing, they thought, would ultimately produce a cement that wasn’t completely smooth. Instead, it would contain small calcium-rich rocks. And little rocks do show up everywhere in the walls of the Romans’ concrete buildings. They might explain how those structures withstood the ravages of time.
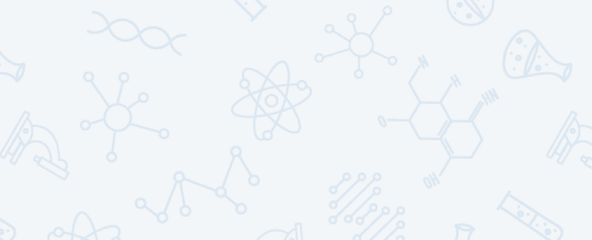
Educators and Parents, Sign Up for The Cheat Sheet
Weekly updates to help you use Science News Explores in the learning environment
Thank you for signing up!
There was a problem signing you up.
Masic’s team had pored over texts by Roman architect Vitruvius and the historian Pliny. Their writings offered some clues. These texts gave strict requirements for the raw materials. For instance, the limestone used to make quicklime must be very pure. And the texts said that mixing quicklime with hot ash and then adding water could make a lot of heat. No rocks were mentioned. Still, the team had a feeling they were important. Every sample of ancient Roman concrete they’d seen held these bits of white rocks, called inclusions.
Where the inclusions came from was unclear for many years, Masic says. Some people suspected the cement just wasn’t fully mixed. But the Romans were super organized. How likely is it, Masic asks, that “every operator [was] not mixing properly, and every single [building] has a flaw?”
What if, his group wondered, these inclusions were a feature of cement, not a bug? The researchers studied the bits embedded at one ancient Roman site. Chemical analysis showed that these inclusions were very rich in calcium.
And that suggested an exciting possibility: The little rocks might be helping the buildings heal themselves. They might be able to patch cracks caused by weathering or even an earthquake. They could supply the calcium needed for a repair. This calcium could dissolve, seep into the cracks and re-crystallize. Then voila! Scar healed.
Hoping nothing explodes
Hot mixing is not how modern cement is made. So the team decided to observe this process in action. Mixing quicklime with water can produce a lot of heat — and possibly an explosion. Although many people thought it was ill-advised, Masic recalls, his team did it anyway.
Step one was to re-create the rocks. They used hot mixing and watched. No big bang occurred. Instead, the reaction produced only heat, a damp sigh of water vapor — and a Roman-like cement mixture bearing small, white, calcium-rich rocks.
Step two was to test this cement. The team created concrete with and without the hot-mixing process and tested the two side-by-side. Each block of concrete was broken in half. The pieces were placed a small distance apart. Then water was trickled through the crack to see if the seepage stopped — and how long it took.
“The results were stunning,” Masic says. The blocks incorporating hot-mixed cement healed within two to three weeks. The concrete produced without hot-mixed cement never healed. The team shared its findings January 6 in Science Advances.
Ancient solution for a modern problem?
Hot mixing’s key role was an educated guess. But now that Masic’s team has cracked the recipe, it could be a boon to the planet.
The Pantheon is an ancient building in Rome, Italy. It and its soaring, detailed, concrete dome have stood for nearly 2,000 years. Modern concrete structures generally last perhaps 150 years, at best. And the Romans didn’t have steel bars (rebar) shoring up their structures.
Concrete manufacturing emits a huge amount of carbon dioxide (CO2) into the air. More frequent replacements of concrete structures means more releases of this greenhouse gas. So longer-lasting concrete could reduce this building material’s carbon footprint.
“We make 4 gigatons per year of [concrete],” Masic says. (A gigaton is one billion metric tons.) Each gigaton equals the weight of some 6.5 million houses. Manufacturing makes as much as 1 metric ton of CO2 per metric ton of concrete. That means concrete is responsible for about 8 percent of global CO2 emissions each year.
The concrete industry is resistant to change, Masic says. For one thing, there are concerns about introducing new chemistry into a tried-and-true process. But “the key bottleneck in the industry is the cost,” he says. Concrete is cheap, and companies don’t want to price themselves out of competition.
This old Roman method adds little cost to making concrete. So Masic’s team hopes that reintroducing this technique could prove a greener, climate-friendly alternative. In fact, they’re banking on it. Masic and several of his colleagues have created a company they call DMAT. It’s seeking funds to start making and selling the Roman-inspired hot-mixed concrete. “It’s very appealing,” the team says, “simply because it’s a thousands-of-years-old material.”